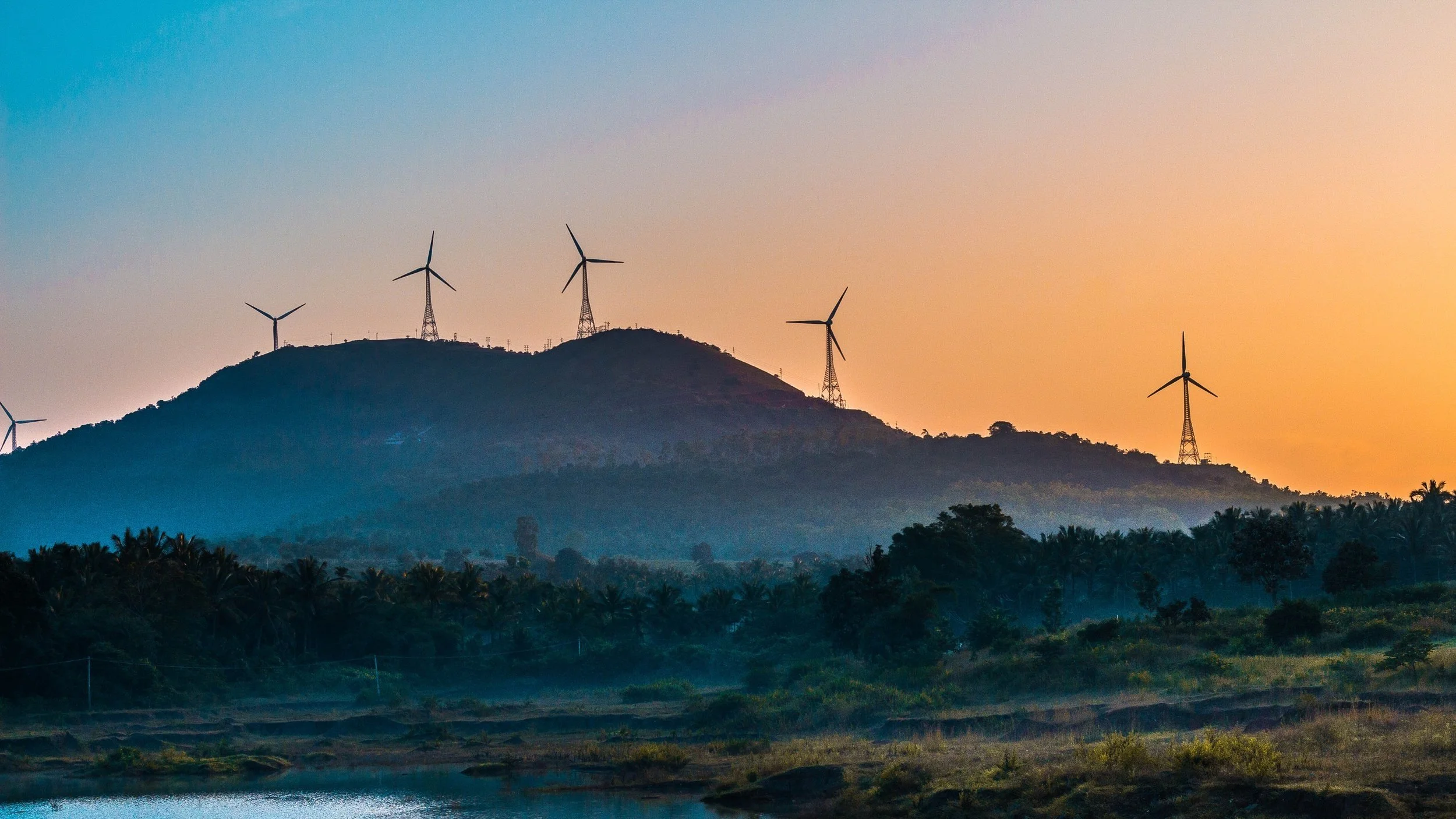
Frequently Asked Questions
VIPER FAQs
-
Did you know that approximately 99% of all electricity storage energy capacity in the United States is actually gravity energy storage? This is in the form of pumped hydro, where water is pumped up a hill to store energy, and then released through a turbine to release that stored energy. This is evidence of the scalability of gravity based energy storage. Gravity is actually very simple, because there are no losses associated with the underlying physics, as compared to compressed air and hydrogen where thermodynamics comes into play.
-
From a first principles perspective, many safety risks can be framed as an “uncontrolled release or conversion of stored energy”. Fires are an uncontrolled conversion of chemical energy into thermal energy. Falls when working at heights and impacts from above are an uncontrolled release of gravitational potential energy through conversion into kinetic energy. Automotive accidents and other impacts are uncontrolled conversion of kinetic energy into work (by squishing things). Pressurised gases (air, methane, hydrogen) can escape in a process called explosion.
-
Not exactly, no. One important feature of batteries is degradation which refers to how the energy storage capacity of batteries degrades, or gets smaller over their lifespan. Most people would have come across this with their smartphone batteries or batteries in other consumer electronics. The thing about degradation is that it’s quite complicated. Calendar degradation refers to degradation that occurs irrespective of battery use, and is a function of cell temperature, cell chemistry and average cell charge. The rate of calendar degradation is increased with increased temperature and with increased state of charge. In other words, a hot battery gets smaller quicker, and a full battery gets smaller quicker. Cycle degradation of batteries refers to degradation that is caused by factors around how much the battery is used, and also how it is used. It is commonly measured by the number of 100% charge-discharge cycles the battery has been subjected to. But it is in fact more complicated than this, because a charge pattern where a battery goes from 100%->0%-100% actually causes significantly more degradation than cycling from 75%->25%->75%->25%->75%, even though both patterns represent a single 100% charge cycle. The mechanism of degradation of batteries is sometimes referred to as “loss of cyclable ions”. The cyclable ions of batteries could be thought of as a moving part similar to a mechanical system, albeit just much smaller and basically impossible to repair or remobilise once “stuck”.
-
In order to function properly, the pumps-turbines up pumped hydro must be situated at the bottom of the lower reservoir, i.e. underground. This also means that the high power electrical equipment must be underground, adding to underground excavation volume and costs. This is contrasted with the VIPER, where the high power electrical equipment is situated above ground.
One benefit of using water in pumped hydro is that water is easy to move between dams in pipes and tunnels with pumps. However this benefit of being easy to move is also a drawback from a safety point of view, because sometimes water can move when you don’t want it to. Dam failures represent catastrophic risks to downstream communities. Water inrush into any underground equipment chamber represents a catastrophic risk to any occupants of the chamber. The presence of catastrophic risks adds to costs, because engineers need to do lots of work and use large safety factors on designs to guarantee the likelihood of an event is as low as possible. The VIPER has the opposite characteristic in this sense. Dirt is by default harder to move than water. But this also means that it is far more stable when stored and far less likely to escape in a catastrophic manner.
An additional consideration for dirt vs water is that dirt is considerably heavier than water, and this means that more energy can be stored in a given purpose built underground excavation. This is important because the construction of the underground storage cavities represents the single largest fraction of the capital cost of the VIPER.
-
No, however it does make a lot of sense to build VIPER systems at underground mines. This is because underground mines already have a valuable asset, which is their access to deep underground. Because of this, the amount of access tunnel required is less than is required for a greenfield VIPER project, reducing the minimum viable project scale. Operating underground mines are also large consumers of electricity, and adding renewables and energy storage can reduce their carbon emissions. Additionally, underground mines which are grid connected can be converted into renewable energy hubs, providing additional value to the mine owner, both financially and also improving their social licence.
-
No. Our budgets include the cost of drilling new mine shafts and constructing new underground cavities. The mine shafts that we need to build are approximately 1 metre in diameter, which is relatively small compared to the 8 metre diameter mine shafts common in the mining industry. The underground storage cavities that we will build are also small compared to the underground cavities built for the turbine halls for pumped hydro facilities.
-
Interestingly, this was not a simple or easy question for us to answer. There are a lot of variables that can influence this, like the revenue model of the project, the desired duration of storage, as well as the cost and technical properties of various components and construction processes. In order to manage all of this complexity, we have built an engineering optimization tool, which uses a long list of mechanical, electrical, energy and mining engineering equations to relate all these parameters to one another. Then, it creates thousands of different design variants using an algorithm known as genetic optimization, to efficiently determine the design that will provide the best commercial returns. Our current model suggests that a depth of 1300 metres (4,265 feet) is optimal for a greenfield VIPER project with 10 hours of storage. As the design duration of storage is increased, the optimal depth also increases, and the average cost and marginal cost per kWh of storage also decreases.
-
We estimate that the VIPER will have a round trip efficiency of 70-75% depending on several factors. This estimate factors in the various sources of energy losses, including those of the motor/generator, gearbox, bucket elevator and belt conveyor equipment.
-
The VIPER is a modular technology, with each module consisting of a surface and an underground stockpile storage site. The surface stockpiles for a standard, 10MW, 120MWh (12 hour) module are approximately 140 metres (460 feet) long and 20 metres (66 feet) wide, with a total of 35,000 tonnes of mobile mass material.
-
A greenfield VIPER project has a minimum size to be commercially attractive, because it must also include the cost to construct the deep underground access tunnel. By the time the VIPER is at the 250MW scale, the decline tunnel becomes only about 10% of the project capital cost, making it a relatively small contributor. 250MW is enough to power approximately 250,000 homes. As compared to large renewable projects that a greenfield VIPER will be colocated with, they are often considerably larger. In the United States, the largest wind farm is 1,548 MW, while the largest solar farm is 802 MW. When considering the land footprint of the VIPER, it is useful to compare it to the footprint required for an equivalently sized solar farm that it might be paired with. A 250 MW solar farm requires 660 hectares (1,630 acres) while a 250MW VIPER with 12 hours of storage would use about 21 hectares (52 acres).
-
There are several different potential types of mass material. Which is used will depend on the cost, availability, material properties and environmental considerations. In cases where it is available, the VIPER may use mine tailings (waste) which is often denser / heavier than normal soil or rocks. With some tailings, we could achieve a material bulk density of up to 2.5 tonnes/m^3. In other cases, the VIPER may use the material that was created during the construction of the underground storage cavities. This can work well because the construction material does not need to be disposed of nor does mass material need to be brought to the site, with the tradeoff that the bulk density is lower at around 1.6 tonnes/m^3.
-
Yes. As the mass material is moved between the surface and underground stockpiles with the storage and release of energy, it experiences attrition. Attrition is the sliding of particles past one another and past other surfaces, and causes the particles to reduce in size and the creation of fines. We take this into consideration at the design phase, by designing all of the bulk material handling equipment to minimise impact velocities, minimise shear velocities and to minimise the pressure at which shearing occurs when material is reclaimed from the stockpiles. The fines that are created are automatically separated from the remainder of the material, and are recycled back into the system after going through a pelletization process.
-
Yes, in fact our initial modelling indicated that steel was the more suitable mass material, while lead was too expensive to justify. Then we learned from experts in the mining industry that the cost of building underground cavities was actually lower than we had first estimated. This changed the optimal material indicated by our optimisation software to be one that was cheaper and less dense such as mine waste or crushed aggregate from the underground chamber construction.
-
The deepest mine in the world is in South Africa, and is approximately 4,000 metres (13,123 feet) deep. The tallest building in the world is the Burj Khalifa at 828 metres (2,717 feet) tall. So the first part of this answer is that we can go a larger distance underground than we can go upwards. The second part of this answer is that for a gravity based energy storage system to be able to store a useful amount of energy for our grids, it needs to use a lot of weight. A greenfield VIPER project with a power capacity of 250MW (~250,000 homes) and 12 hours of storage, would need 25 of our 10MW VIPER modules. Each VIPER module has 35,000 tonnes of mobile mass, for a total project mobile mass of 875,000 tonnes. For reference, the world’s tallest building, the Burj Khalifa weighs 500,000 tonnes. So, based on this preliminary assessment, it seems unlikely that a tall building could hold enough weight in a way that’s economically, environmentally and structurally feasible. Comparing this to the VIPER, all of the weight sits on the ground, which is easily strong enough.
-
The VIPER is extremely environmentally friendly when compared to alternatives like Lithium ion batteries and pumped hydro. There are a handful of important metrics for this including embodied energy, embodied CO2, embodied long-lived waste and ecological impacts.
The first metric, embodied CO2 refers to the CO2 that is emitted during the creation of the energy storage technology, including emissions from electricity and from other chemical or industrial processes. The VIPER uses very little steel or concrete (unlike pumped hydro and several other gravity energy storage technologies), materials which are CO2 intensive with processes that will take decades to decarbonise.
The second metric, embodied energy, is the amount of energy that is required to manufacture, construct and operate the energy storage facility, relative to how much energy it can store and release over its lifetime. This is sometimes called Energy Stored On Energy Invested (ESOEI). The ESOEI of Li-Ion batteries is estimated at 32, while the ESOEI of pumped hydro is estimated at 704 (source). We have not yet finished our calculations for the ESOEI of VIPER, however we expect it to be much closer to pumped hydro than batteries. The concept of ESOEI and EROI are first principles lenses to the world’s energy system. If we want cheap, abundant and clean energy, it’s important that we don’t spend too much of that energy just maintaining the energy system.
The third metric, the embodied long-lived waste, refers to the waste that is created during the manufacturing, construction and operation of the energy storage technology that is stored in landfill. This is particularly significant for batteries like Li-ion that use metals like Copper and Aluminium, as for each kilogram of metal used, 100’s of kilograms of chemically toxic waste is created. By contrast, the main storage medium of the VIPER is just dirt, which can be returned to the underground storage site for decommissioning.
The fourth metric is the ecological impacts of the storage technology, and refers to the consumption or destruction of natural habitats of various forms of life. Pumped hydro often involves the damming of rivers or valleys, or the construction of dams atop mountains, areas which are usually extremely ecologically diverse. Additionally, because the best pumped hydro sites are often distant from existing grid infrastructure, connecting them to the grid can also involve large easements for transmission infrastructure through national parks. Mining for metals used in batteries is often conducted with huge open cut mines in areas which may have had considerable ecological diversity. In contrast, because greenfield VIPER projects can be built just about anywhere, locations can be selected that have low biodiversity and therefore much lower ecological impacts.
-
The VIPER has been conceptualised with a strong understanding of the mechanics of reliability, as well as the capabilities of digital sensors for asset health monitoring. While the VIPER does have a lot of moving parts, particularly in the bucket elevator, the design of the bucket elevator means that it has a low number of unique moving parts. This is important, because it means that design effort that goes toward making these parts highly reliable is relatively small and is used many times. Furthermore, testing of new designs at small scale allows us to demonstrate reliability of these designs prior to large scale deployment.
-
No. The VIPER has no coupling between state of charge or depth of discharge and long term health like batteries do. It can be kept “full” during times of extended renewable wind or solar availability without causing accelerated degradation like with batteries. Similarly, it can be fully “emptied” or moved through any pattern of charge and discharge without need for concern about impacts to health. Note that the terminology of “charge” and “discharge” is not technically correct in the context of the VIPER, however it is terminology that is familiar to most people because it is correct for batteries.
-
The extent to which ground water ingress is an issue differs from site to site. The rate that water enters the underground excavations depends on the water table level and the permeability of the bedrock. This rate of water ingress can be reduced by the injection of grout into the joints in the bedrock, as is routinely done in underground mines. The groundwater removal system is designed to only run the pumps and consume energy when there is surplus renewable energy, making the cost of removing it a minimal expense. The rate of groundwater ingress is higher initially, before stabilising at a lower amount after several months.
-
We are working on several potential sites to host the first physical demonstration of the VIPER technology in the underground environment. Requirements for a pilot site are access to underground depth of at least 100 metres (328 ft). Most of our candidate sites are existing underground mines.